If you’re planning your next DIY project and are considering using JB Weld as your bonding agent, you may be wondering, “What will JB Weld not stick to?” While this two-part epoxy adhesive is known for its versatility and strength in bonding various materials, there are some surfaces that it may not adhere to effectively.
For example, some plastics with high oil content, Teflon, silicone, and certain rubber materials may not be suitable for JB Weld. To avoid potential adhesion issues, it’s essential to read the manufacturer’s instructions carefully and conduct some research to determine if JB Weld is the right choice for your specific project and materials.
Let’s dive into this peculiar topic and uncover the taste, health risks, and even unique uses of glue beyond its intended purpose.
Knowing what materials JB Weld will and won’t bond with can save you time and effort, and help ensure that your project is a success. Keep reading to learn more about what materials JB Weld may not stick to and how to use it effectively.
What Will JB Weld Not Stick To?
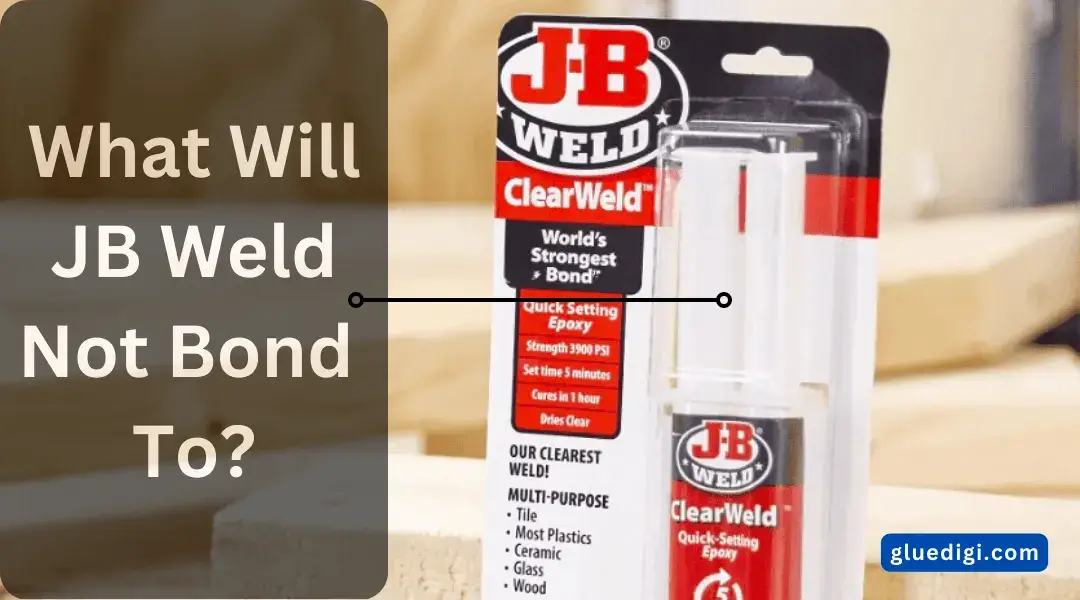
JB Weld is a two-part epoxy that is designed to bond a variety of materials. However, there are some surfaces that JB Weld will not adhere to. These include:
- Teflon: Teflon is a smooth and non-porous material that is resistant to adhesives. JB Weld will not stick to Teflon surfaces.
- Silicone: Silicone is a flexible and rubber-like material that is also resistant to adhesives. JB Weld will not stick to silicone surfaces.
- Polyethylene and polypropylene: These plastics are low-surface-energy plastics, meaning that they are not conducive to bonding. JB Weld will not stick to polyethylene and polypropylene surfaces.
- Oil and grease: Oily and greasy surfaces are also resistant to adhesion. JB Weld should be thoroughly cleaned and dried before application to ensure maximum adhesion.
How To Apply JB Weld?
The application of JB Weld is a simple process that requires the following steps:
Mix the epoxy:
JB Weld comes in two parts, the resin and the hardener. These two parts should be mixed thoroughly to ensure an even and consistent bond.
Clamp the surfaces together:
The two surfaces should be clamped together tightly to ensure maximum adhesion. The clamping pressure should be maintained for at least 4-6 hours.
Allow to cure:
JB Weld takes 15-24 hours to cure completely. The bond will be strongest after a full cure time of 15-24 hours.
JB Weld In Use: Some Examples
JB Weld is a versatile adhesive that has a wide range of applications and can bond various materials. One of the most common uses of JB Weld is to repair cracks in metal objects such as cast iron, aluminum, and steel. Additionally, it can be used to bond dissimilar materials such as metal to plastic or wood to metal.
Another useful application of JB Weld is to repair damaged threads in bolts, nuts, and other threaded objects. It can also be used to seal leaks in pipes, radiators, and other objects that contain fluids. Overall, JB Weld is a popular choice for DIY enthusiasts and professionals alike due to its high strength and versatility.
How Do You Make JB Weld NOT Stick?
There are some steps you can take to prevent JB Weld from sticking to a surface. One option is to apply a release agent like vegetable oil or silicone spray on the surface before applying the JB Weld. Another method is to use a barrier like plastic wrap or masking tape to cover the surface area that you don’t want the JB Weld to stick to.
Finally, a separating agent such as petroleum jelly or Vaseline can be applied to the surface to prevent adhesion. These techniques can be useful in situations where you need to apply JB Weld to a specific area without it sticking to other areas or surfaces. However, it’s important to note that these techniques may affect the overall strength of the bond, and it’s always recommended to follow the manufacturer’s instructions for the best results
Does Glue Expire? What Should You Do
How Do You Make JB Weld NOT Stick?
If you want to make JB Weld not stick to a surface, there are a few steps that you can follow. These include:
Use a barrier:
A barrier such as plastic wrap or masking tape can be applied to the surface to prevent the JB Weld from adhering.
Use a separating agent:
A separating agent such as petroleum jelly or Vaseline can be applied to the surface to prevent the JB Weld from adhering.
Why Does JB Weld Not Stick To Plastic?
JB Weld does not stick to plastic because plastic is a low-surface-energy material. Low-surface-energy materials are not conducive to bonding, meaning that adhesives do not adhere well to these surfaces. Additionally, many plastics are smooth and non-porous, making it difficult for the epoxy to grip and form a strong bond. To increase the chances of adhesion to plastic, the surface should be thoroughly cleaned and roughed up with sandpaper or a similar abrasive material.
Does Hot Glue Work on Fabric?
Does Glue Stick to Parchment Paper?
Will The JB Weld Adhere To Itself?
Yes, JB Weld can adhere to itself. This means that if a small amount of epoxy is mixed and applied to itself, it will cure and form a solid bond. This property can be handy for shaping and building up small amounts of epoxy in some repair scenarios.
Conclusion
JB Weld is a dependable bonding agent suitable for various projects such as repairing metal cracks and sealing pipe leaks. However, it may not adhere to certain surfaces. To prevent adhesion issues, it’s essential to know what JB Weld will not stick to. To ensure a robust and enduring bond, carefully follow the manufacturer’s instructions and prepare the surfaces correctly. DIY enthusiasts and professionals alike choose JB Weld for its strength and versatility. Try it out on your next project and experience the benefits of this potent adhesive firsthand.