The rubberized adhesive is a versatile and widely used adhesive that offers excellent adhesion, durability, and flexibility. It is commonly employed in various industries due to its unique properties and ability to bond different materials.
Let’s dive into this peculiar topic and uncover the taste, health risks, and even unique uses of glue beyond its intended purpose.
In this comprehensive guide, we will delve into the world of rubberized adhesive, exploring its composition, types, applications, advantages, limitations, safety considerations, and tips for optimal use. Also, you will get Wood Veneer Adhesive: The Ultimate Woodworking Game-Changer!
Understanding Rubberized Adhesive
The rubberized adhesive is a type of adhesive that contains rubber as one of its main components. It is formulated to provide strong and durable bonds, especially on rubber surfaces.
The composition of rubberized adhesives typically includes rubber polymers, resins, solvents, and additives. These components work together to create a sticky and cohesive substance capable of bonding various materials.
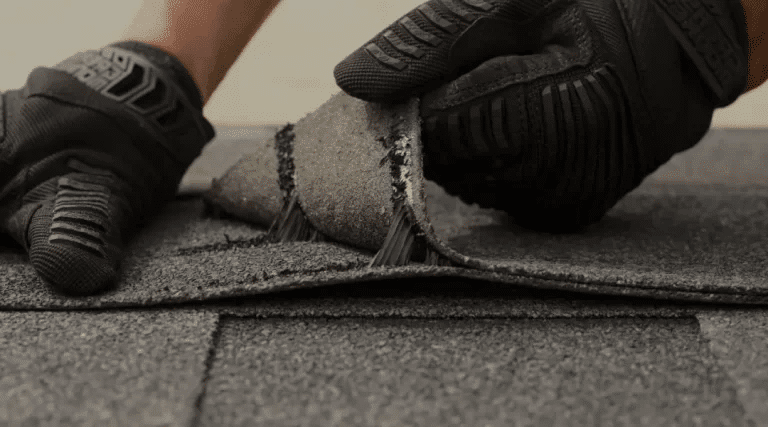
Key Characteristics and Properties
The rubberized adhesive exhibits several key characteristics and also properties that make it highly desirable for numerous applications. Some of these include:
- Excellent adhesion to rubber surfaces: Rubberized adhesive is specifically designed to adhere well to rubber materials, ensuring a secure and long-lasting bond.
- Provides strong and durable bonds: This type of adhesive forms robust bonds that withstand stress, vibration, and environmental factors, contributing to the overall strength and longevity of the bonded objects.
- Flexible and resilient: Rubberized adhesive offers flexibility and also resilience, allowing for movement and stress absorption without compromising the bond.
- Resistant to water, oil, and other common chemicals: Rubberized adhesive demonstrates resistance to various substances, making it suitable for applications in environments where exposure to liquids and chemicals is likely.
- Withstands high temperatures and extreme weather conditions: It possesses the ability to maintain its adhesive properties under elevated temperatures and adverse weather conditions, making it suitable for outdoor and high-temperature applications.
- Offers vibration and shock absorption properties: Rubberized adhesive can absorb vibrations and shocks, making it ideal for applications that involve movement or machinery.
- Provides good electrical insulation: It possesses insulating properties, making it suitable for electrical applications where a strong bond and electrical insulation are required.
- Can fill gaps and irregularities, ensuring a tight seal: Rubberized adhesive has the ability to fill gaps and irregularities, creating a secure and airtight seal between bonded surfaces.
- Easy to apply and work with: This adhesive is typically available in various forms such as tapes, sprays, and liquids, making it convenient and easy to apply to different materials.
- Suitable for a wide range of materials: Rubberized adhesive is compatible with various materials, including rubber, plastics, metals, and fabrics, making it versatile for use in different industries and applications.
Different Types of Rubberized Adhesive
Rubberized adhesive comes in different formulations to meet specific application requirements. Some of the common types include:
- Neoprene adhesive: Neoprene adhesive is known for its excellent resistance to oil, chemicals, and extreme temperatures. It is widely used in the automotive and manufacturing industries.
- Silicone rubber adhesive: Silicone rubber adhesive offers excellent resistance to high temperatures, weathering, and UV radiation. It finds applications in the electronics, medical, and aerospace industries.
- Butyl rubber adhesive: Butyl rubber adhesive provides exceptional resistance to water, chemicals, and gases. It is commonly used in construction and automotive applications.
- Polyurethane rubber adhesive: Polyurethane rubber adhesive exhibits excellent flexibility, high bond strength, and resistance to environmental factors. It is utilized in construction, marine, and automotive industries.
- Natural rubber adhesive: Natural rubber adhesive offers good adhesion and flexibility. It is commonly used in the footwear and textile industries.
- Styrene-butadiene rubber adhesive: Styrene-butadiene rubber adhesive provides excellent adhesion and is widely used in the packaging industry.
- Ethylene propylene diene monomer (EPDM) adhesive: EPDM adhesive offers excellent resistance to weathering, ozone, and chemicals. It is commonly used in the automotive and construction industries.
- Acrylic rubber adhesive: Acrylic rubber adhesive provides high bond strength and good resistance to weathering and chemicals. It is utilized in various industries, including construction and electronics.
- Nitrile rubber adhesive: Nitrile rubber adhesive offers excellent resistance to oil, fuel, and chemicals. It is commonly used in the automotive and manufacturing industries.
- Hypalon adhesive: Hypalon adhesive is known for its exceptional resistance to chemicals, weathering, and extreme temperatures. It finds applications in the marine and aerospace industries.
Applications of Rubberized Adhesive
Rubberized adhesive finds wide-ranging applications across various industries. Some of the key sectors where it is utilized include:
Automotive Industry
In the automotive industry, rubberized adhesive is used for bonding rubber seals, gaskets, trims, and panels. It ensures a secure and long-lasting bond, even under high temperatures and exposure to automotive fluids.
Construction Industry
Rubberized adhesive plays a vital role in the construction industry for bonding roofing materials, flooring, insulation, and sealing joints. It provides a strong and flexible bond that withstands extreme weather conditions and provides excellent water resistance.
Electronics Industry
Rubberized adhesive is employed in the electronics industry for bonding components, securing cables, and providing electrical insulation. Its resistance to high temperatures and good electrical insulation properties make it ideal for electronic applications.
Manufacturing Industry
In the manufacturing industry, rubberized adhesive is used for bonding various components, assembling products, and providing airtight seals. It enhances the efficiency and durability of manufactured goods.
Medical Industry
Rubberized adhesive is utilized in the medical industry for securing dressings, bandages, and medical devices. Its hypoallergenic properties and ability to adhere well to skin make it suitable for medical applications.
Marine Industry
Rubberized adhesive finds extensive use in the marine industry for bonding boat parts, sealing joints, and repairing inflatable boats. Its resistance to water and extreme weather conditions makes it a reliable choice in marine environments.
Aerospace Industry
Rubberized adhesive is employed in the aerospace industry for bonding aircraft components, sealing fuel tanks, and providing insulation. Its ability to withstand extreme temperatures and resistance to chemicals are critical in aerospace applications.
Sporting Goods Manufacturing
In the manufacturing of sporting goods, rubberized adhesive is used for bonding equipment components, securing grips, and assembling parts. It provides durability and flexibility, ensuring reliable performance.
Footwear Industry
Rubberized adhesive plays a significant role in the footwear industry for bonding shoe soles, securing insoles, and assembling different parts. Its excellent adhesion to rubber and flexibility make it a popular choice in shoe manufacturing.
Textile Industry
In the textile industry, rubberized adhesive is utilized for bonding fabrics, creating waterproof seams, and adding protective coatings. It enhances the durability and functionality of textiles.
Packaging Industry
Rubberized adhesive is essential in the packaging industry for sealing boxes, securing labels, and bonding various packaging materials. Its adhesive properties ensure reliable and tamper-evident packaging.
HVAC (Heating, Ventilation, and Air Conditioning) Industry
In the HVAC industry, rubberized adhesive is used for bonding insulation, sealing ducts, and securing components. Its ability to withstand temperature fluctuations and resist chemicals is vital in HVAC applications.
General Household Repairs
Rubberized adhesive finds its place in general household repairs for fixing
rubber objects, repairing leaks, and securing loose parts. It offers a convenient and reliable solution for various repair tasks.
DIY Projects
Rubberized adhesive is a popular choice for DIY enthusiasts for various projects such as crafting, repairs, and customization. Its versatility and ease of use make it suitable for a wide range of applications.
Art and Craft Projects
Rubberized adhesive is widely used in art and craft projects for bonding different materials, such as paper, fabric, and rubber. Its strong adhesive properties and flexibility enable artists and crafters to create durable and visually appealing projects.
Advantages of Rubberized Adhesive
Rubberized adhesive offers several advantages that contribute to its popularity and wide usage. These advantages include:
- Excellent adhesion to rubber surfaces: Rubberized adhesive forms strong bonds with rubber materials, ensuring a secure and long-lasting connection.
- Provides strong and durable bonds: The adhesive creates robust bonds that withstand stress, vibrations, and environmental factors, ensuring the longevity of the bonded objects.
- Flexible and resilient: Rubberized adhesive remains flexible and resilient after bonding, allowing for movement and stress absorption without compromising the bond’s integrity.
- Resistant to water, oil, and other common chemicals: It exhibits resistance to liquids and chemicals, making it suitable for applications where exposure to such substances is likely.
- Withstands high temperatures and extreme weather conditions: Rubberized adhesive maintains its adhesive properties under elevated temperatures and adverse weather conditions, ensuring reliable performance in various environments.
- Offers vibration and shock absorption properties: The adhesive can absorb vibrations and shocks, making it ideal for applications involving movement or machinery.
- Provides good electrical insulation: Rubberized adhesive possesses insulating properties, making it suitable for electrical applications where a strong bond and electrical insulation are required.
- Can fill gaps and irregularities, ensuring a tight seal: The adhesive has the ability to fill gaps and irregularities between bonded surfaces, creating a secure and airtight seal.
- Easy to apply and work with: Rubberized adhesive is available in various forms, such as tapes, sprays, and liquids, making it convenient and straightforward to apply to different materials.
- Suitable for a wide range of materials: Rubberized adhesive is compatible with various materials, including rubber, plastics, metals, and fabrics, offering versatility and adaptability in different applications.
- Enhances overall product performance and longevity: The adhesive improves the performance and durability of products by providing strong and reliable bonds between materials.
Limitations of Rubberized Adhesive
While rubberized adhesive offers numerous advantages, it also has some limitations that should be taken into consideration:
- Limited temperature resistance: Rubberized adhesive may have temperature limitations, and excessive heat or extreme cold can affect its performance.
- Susceptibility to aging: Over time, rubberized adhesive may deteriorate, losing some of its adhesive properties. Proper storage and handling can help prolong its shelf life.
- Limited solvent resistance: Certain solvents can weaken or dissolve rubberized adhesive, affecting its bonding capabilities.
- Reduced adhesion on certain surfaces: While rubberized adhesive adheres well to many materials, there are specific surfaces or coatings where its adhesion may be compromised.
- Limited compatibility with certain materials: Rubberized adhesive may not be compatible with all materials, requiring careful consideration when selecting the adhesive for specific applications.
- Longer curing or drying time compared to other adhesives: Rubberized adhesive may require more time to cure or dry compared to other adhesives, which should be factored into project timelines.
- Vulnerability to moisture and water damage: Excessive exposure to moisture or water can weaken or damage rubberized adhesive, impacting its adhesive properties.
- Limited flexibility in some applications: While rubberized adhesive offers flexibility, there may be applications where its level of flexibility may not be sufficient.
- Not suitable for high-stress or heavy-load applications: Rubberized adhesive may not be the best choice for applications that involve high stress or heavy loads, where specialized adhesives may be required.
- Potential for shrinkage or expansion over time: Rubberized adhesive may experience minor dimensional changes, such as shrinkage or expansion, which should be considered in precise applications.
Safety Considerations
When working with rubberized adhesive, it is important to consider the following safety precautions:
- Ensure proper ventilation in the working area: Rubberized adhesive may emit fumes or vapors, so working in a well-ventilated area is essential to minimize exposure.
- Wear appropriate personal protective equipment (PPE): Protective gloves, safety goggles, and a respirator should be worn to protect against potential skin contact, eye irritation, and inhalation of fumes.
- Avoid direct skin contact with the adhesive: Rubberized adhesive may cause skin irritation or sensitization, so it is crucial to avoid direct contact. If accidental contact occurs, wash the skin immediately with soap and water.
- Use safety goggles to protect your eyes from any splashes or fumes: Safety goggles should be worn to shield the eyes from potential contact with the adhesive or any splashes that may occur during application.
Choosing the Right Rubberized Adhesive
Selecting the appropriate rubberized adhesive for a specific application involves considering several factors:
- Factors to consider when selecting an adhesive: Factors such as the materials being bonded, environmental conditions, temperature range, flexibility requirements, and intended use should be taken into account.
- Matching adhesive properties with specific applications: Identifying the desired characteristics, such as temperature resistance, flexibility, or chemical resistance, and selecting an adhesive that matches those requirements is crucial for successful bonding.
- Popular brands and their offerings: There are various reputable brands in the market that offer a range of rubberized adhesives. Researching and selecting a trusted brand can help ensure the quality and reliability of the adhesive.
Tips for Applying Rubberized Adhesive
To achieve optimal results when working with rubber adhesive, the following tips should be kept in mind:
- Clean the surface thoroughly: The surfaces being bonded should be clean, dry, and free from any dirt, grease, or contaminants that may interfere with adhesion.
- Apply adhesive evenly: The adhesive should be applied evenly across the bonding surfaces to ensure a consistent bond.
- Use the right amount of adhesive for the job: Applying too little adhesive may result in a weak bond, while using excessive adhesive may lead to messy application and longer curing times.
- Allow sufficient drying/curing time: Following the manufacturer’s instructions, allow the adhesive sufficient time to dry or cure to achieve maximum bond strength.
- Apply pressure to ensure a strong bond: Applying pressure to the bonded surfaces helps promote better contact and enhances the adhesive’s ability to create a strong bond.
- Avoid excessive handling or movement during the drying/curing process: Excessive movement or handling of bonded objects during the drying or curing process may disrupt the bond formation, leading to weaker adhesion.
- Follow the recommended temperature and humidity conditions: Adhesive performance can be affected by temperature and humidity, so it is important to follow the recommended conditions for optimal bonding.
- Clean up any excess adhesive promptly: Promptly removing any excess adhesive before it dries or cures helps maintain a neat and tidy appearance while preventing unwanted adhesion to unintended areas.
Rubberized Adhesive vs. Other Adhesive Types
ing rubberized adhesive to other adhesive types can help in selecting the most suitable adhesive for specific applications. Here are some factors to consider:
Bonding Strength
Rubberized adhesive provides excellent bonding strength, especially on rubber surfaces. It is specifically formulated for optimal adhesion to rubber materials. Comparatively, other adhesives may excel in bonding different materials but may not offer the same level of adhesion on rubber surfaces.
Application Flexibility
Rubberized adhesive offers flexibility and resilience, allowing for movement and also stress absorption. This makes it suitable for applications that involve bending, twisting, or vibration. Other adhesive types may have varying degrees of flexibility depending on their formulation and also intended use.
Resistance to Environmental Factors
The rubberized adhesive is known for its resistance to water, oil, chemicals, high temperatures, and extreme weather conditions. It maintains its adhesive properties in challenging environments. Other adhesives may have different resistance capabilities, depending on their formulation and also intended use.
Flexibility and Elasticity
Rubberized adhesive exhibits flexibility and also elasticity, enabling it to accommodate movements and stresses without compromising the bond. Other adhesives may have different levels of flexibility and elasticity, depending on their formulation and intended application.
Curing Time and Speed
A rubber adhesive may require a longer curing or drying time compared to other adhesives. Some adhesives offer faster curing times or also instant bonding capabilities, which can be advantageous for time-sensitive projects.
Compatibility with Materials
The rubber adhesive is compatible with a wide range of materials, including rubber, plastics, metals, and fabrics. Other adhesive types may have specific compatibility with certain materials, requiring careful consideration when selecting the adhesive for specific applications.
Ease of Use and Cleanup
Rubber adhesive is typically available in various user-friendly forms such as tapes, sprays, and liquids, making it easy to apply to different materials. Cleanup of excess adhesive can be done promptly with appropriate solvents or cleaning agents. Other adhesive types may have different application methods and cleanup requirements.
Conclusion
The rubberized adhesive is a valuable and also versatile used across multiple industries for its excellent adhesion, durability, and also flexibility. Its ability to bond rubber surfaces effectively, coupled with its resistance to water. Chemicals, and also extreme temperatures, make it an ideal choice for various applications.
By understanding its composition, types, applications, advantages, limitations, safety considerations, and best practices. Users can harness the full potential of rubber adhesive in their projects. Whether it’s in automotive, construction, electronics, or household repairs. Rubber adhesive proves to be an indispensable tool in enhancing product performance and ensuring reliable bonds.