Welcome to the realm of metal-filled adhesive – your key to unleashing the extraordinary potential of metallic bonding. This remarkable adhesive combines the strength and durability of metals with the versatility and ease of application of adhesive.
Imagine a world where bonds are unbreakable, where metals unite with unparalleled strength, and where the power of metallic bonding knows no bounds.
It opens up a world of possibilities in various industries and applications, from manufacturing and construction to automotive and electronics. In this blog post, we will delve into the captivating world of metal-filled adhesive, exploring its uses, benefits, and the incredible power it holds to revolutionize bonding like never before.
Get ready to witness the magic of metallic bonding unleashed with metal-filled adhesive!
Definition of Metal-filled Adhesive
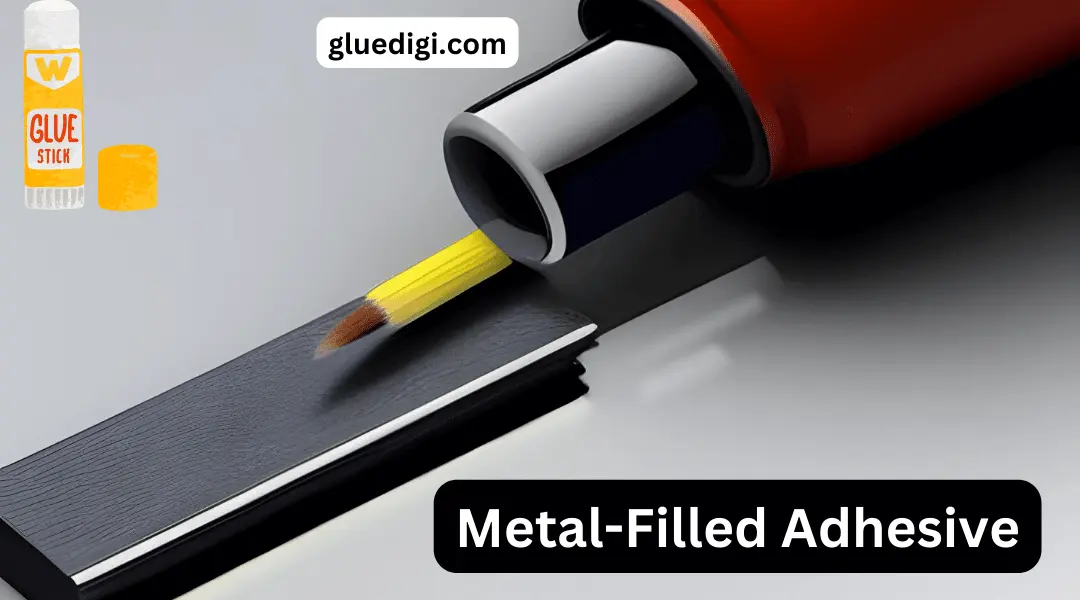
Metal-filled adhesive is a specialized type of adhesive that incorporates metallic particles or flakes into its formulation. This unique adhesive composition combines the strength and durability of metals with the versatility and ease of use of adhesives. It forms a strong and reliable bond between metal surfaces, surpassing traditional joining methods like welding or mechanical fastening.
The metal fillers enhance the adhesive’s mechanical properties, including tensile strength and resistance to impact and vibration. Metal-filled adhesives are widely use in industries such as automotive, aerospace, electronics, and construction. Offering a cost-effective and efficient solution for bonding different types of metals together, as well as eliminating the need for labor-intensive processes like drilling or welding.
Composition of Metal-filled Adhesive
Metal-filled adhesives are formulate by combining various components to achieve a strong and durable bond. The composition typically includes:
Metal Particles
Metal-filled adhesives contain finely dispersed metal particles, such as aluminum, copper, or steel. These particles enhance the adhesive’s mechanical strength and conductivity.
Polymer Resin
A polymer resin serves as the adhesive matrix, providing cohesion and adhesion properties. Common resin systems used include epoxy, polyurethane, or acrylic, which offer excellent bonding strength and resistance to environmental factors.
Fillers and Reinforcements
Fillers and reinforcements, such as silica, glass fibers, or carbon nanotubes, may be incorporate to enhance the adhesive’s mechanical properties, including stiffness, impact resistance, and thermal conductivity.
Solvents and Catalysts
Solvents and catalysts are added to facilitate the adhesive’s application and curing process. The Solvents aid in reducing viscosity for easier handling, while catalysts initiate the chemical reaction that enables the adhesive to harden and create a strong bond.
Additives and Stabilizers
Various additives and stabilizers may be included to improve the adhesive’s performance and stability. These additives can enhance properties like flexibility, UV resistance, chemical resistance, and shelf-life stability.
Uses of Metal-filled Adhesive
Like a versatile tool in a handyman’s toolbox, the metal-filled adhesive has found its way into various industries, offering a strong bonding solution for materials that require a combination of metal properties and adhesive strength. The uses of metal-filled adhesives are vast and diverse, and they are often found in industrial settings where high-strength bonding is required.
Repairing Metal Surfaces
Metal-filled adhesive is commonly used for repairing damaged or corroded metal surfaces, providing a strong and durable bond.
Creating Metal-to-Metal Bonds
This adhesive is ideal for creating secure metal-to-metal bonds, whether for joining two metal pieces or reinforcing existing connections.
Filling Metal Cavities or Gaps
Metal-filled adhesive can effectively fill cavities, gaps, or voids in metal components, restoring structural integrity.
Restoring Worn-out Threads
By applying metal-filled adhesive to worn-out or damaged threads, they can be restored and strengthened, extending the lifespan of the metal object.
Conductive Traces for Electronics
Metal-filled adhesive with conductive properties is used in electronics to create conductive traces, making it an excellent alternative to soldering.
Bonding Metal Components with Other Materials
Metal-filled adhesive enables the bonding of metal components to other materials, such as plastic, glass, or wood, expanding its application versatility.
Repairing Cracks or Breaks in Metal Objects
Cracked or broken metal objects can be effectively repaired using metal-filled adhesive, restoring their functionality and appearance.
Reinforcing Weld Joints
Metal-filled adhesive acts as a supplementary reinforcement for weld joints, enhancing their strength and durability.
Sealing Metal Surfaces
Metal-filled adhesive can be used as a sealant for metal surfaces, providing protection against moisture, chemicals, and other environmental factors.
Mounting Metal Hardware
Metal-filled adhesive is commonly employed for mounting metal hardware, such as brackets, hooks, or handles, securely attaching them to various surfaces.
Pros of Metal-filled Adhesive
The Metal-filled adhesive has various advantages that make it an exceptional choice for various industrial applications.
Superior Strength and Durability
Metal-filled adhesive provides exceptional strength and durability, making it ideal for high-stress applications where a reliable bond is crucial.
Excellent Heat Resistance
With its ability to withstand high temperatures, metal-filled adhesive is well-suited for bonding metal components that experience heat exposure.
Electrical Conductivity
Metal-filled adhesive maintains electrical conductivity, enabling it to create reliable electrical connections between metal parts.
Chemical Resistance
Metal-filled adhesive demonstrates resistance to various chemicals, ensuring the integrity of bonded joints even in harsh environments.
Enhanced Structural Integrity
By filling gaps and voids, metal-filled adhesive enhances the structural integrity of assemblies, providing stability and support.
Versatile Compatibility
Metal-filled adhesive is compatible with a wide range of metals, including steel, aluminum, copper, and brass, facilitating diverse bonding applications.
Efficient Repair Solution
It serves as an effective repair solution for metal components, allowing for quick and reliable fixes, reducing downtime and costs.
Impact and Vibration Resistance
The adhesive’s high resistance to impact and vibration helps maintain the integrity of bonded joints, even in dynamic and demanding conditions.
Corrosion Prevention
Metal-filled adhesive forms a protective barrier, preventing corrosion and extending the lifespan of metal structures or components.
Easy Application and Curing
With its user-friendly application and relatively quick curing time, metal-filled adhesive offers convenience and efficiency in bonding processes.
Enhanced Machinability
Metal-filled adhesive often possesses good machinability, allowing for post-bonding processes such as drilling, tapping, or machining without sacrificing bond integrity.
Resistance to Moisture and Humidity
Metal-filled adhesive exhibits resistance to moisture and humidity, making it suitable for applications where exposure to water or humid conditions is expected.
Reduced Weight
Compared to traditional metal joining methods like welding, metal-filled adhesive offers a lightweight alternative, enabling weight reduction in assembled structures or components.
Improved Aesthetics
Metal-filled adhesive can create clean, seamless bonds, enhancing the visual appeal of metal assemblies by eliminating the need for visible fasteners or weld marks.
Cons of Metal-filled Adhesives
Drawbacks of this type of adhesive include the potential for decreased bonding strength compared to non-metal-filled alternatives, which may limit its usefulness in certain applications.
Limited Temperature Resistance
Metal-filled adhesive may have limited temperature resistance, leading to potential weakening or failure of the bond under high heat or extreme cold conditions.
Reduced Flexibility
The presence of metal particles in the adhesive can reduce its overall flexibility, making it less suitable for applications that require significant movement or flexibility.
Increased Weight
Metal-filled adhesive can add additional weight to the bonded parts, which may not be desirable in applications where weight is a concern.
Potential Electrical Conductivity
Depending on the metal particles used, metal-filled adhesive may have electrical conductivity properties that can interfere with electrical components or circuits if not properly isolated.
Higher Cost
Metal-filled adhesive tends to be more expensive compared to standard adhesives due to the inclusion of metal particles, making it less cost-effective for certain projects.
Limited Transparency
Metal-filled adhesive is typically opaque or partially opaque, which can be a disadvantage if transparency or invisibility is desired in the bonded area.
Susceptible to Corrosion
If the metal particles within the adhesive are not corrosion-resistant, the adhesive bond may be prone to corrosion over time, compromising its integrity.
Potential Difficulty in Surface Preparation
Achieving proper surface preparation for metal-filled adhesive bonding can be more challenging compared to standard adhesives, as metal surfaces often require special cleaning or treatment.
Longer Curing Time
Metal-filled adhesive may require longer curing time compared to standard adhesives, which can prolong the overall project timeline.
Limited Availability of Metal Types
The availability of metal-filled adhesives may be limited to specific types of metal particles, reducing the range of options for specific bonding requirements.
Considerations for Choosing Metal Adhesive
Despite its numerous benefits, the metal-filled adhesive also has its downsides, which can negatively impact its use in certain applications. One of the main cons of metal-filled adhesive is that it can be brittle and prone to cracking, especially when exposed to high levels of stress or extreme temperatures.
Additionally, it can be challenging to remove and replace metal adhesive once it has been applied, making it a less flexible choice for applications that require frequent changes or adjustments.
Material Compatibility
Select an adhesive that is compatible with the metal surfaces you plan to bond. Different metals may have varying properties, such as reactivity or surface roughness, which can affect adhesive performance. Ensure the adhesive is specifically designed for bonding the metals in your application.
Bond Strength
Evaluate the required bond strength for your project. Consider factors such as load-bearing capacity, temperature fluctuations, and environmental conditions. Choose a metal-filled adhesive with sufficient strength to withstand the anticipated stresses and maintain a reliable bond over time.
Cure Time
Determine the desired cure time for your application. Some metal-filled adhesives offer fast curing options, while others may require longer curing periods for optimal bonding strength. Consider the assembly process and project timeline to ensure the adhesive’s cure time aligns with your needs.
Thermal and Chemical Resistance
Assess the environmental conditions the adhesive will encounter. If the bonded assembly will be exposed to high temperatures or chemicals, select a metal-filled adhesive with excellent thermal and chemical resistance. This will ensure the adhesive maintains its bond integrity and mechanical properties under challenging conditions.
Application Method
Consider the application method that suits your project best. Metal-filled adhesives are available in various forms, such as liquids, pastes, or films. Choose an adhesive that aligns with your preferred application method, whether it’s brush, spray, or dispensing.
Adhesive Handling and Storage
Check the adhesive’s handling and storage requirements. Some metal-filled adhesives may have specific temperature, humidity, or shelf-life requirements. Ensure you can meet these conditions to maintain the adhesive’s effectiveness and prolong its shelf life.
Safety Considerations
Review the safety guidelines provided by the adhesive manufacturer. Take precautions such as wearing protective equipment, working in well-ventilated areas, and following proper handling and disposal procedures. Prioritize adhesives that have low toxicity and emit minimal volatile organic compounds (VOCs) for a safer working environment.
Test and Validation
Conduct testing and validation to ensure the selected metal-filled adhesive meets your performance requirements. Perform trials on representative samples to assess bond strength, durability, and compatibility with other materials or coatings used in the assembly.
Technical Support
Consider the availability of technical support from the adhesive manufacturer. Having access to knowledgeable experts can be invaluable for troubleshooting, guidance on application techniques, and addressing any questions or concerns that may arise during the bonding process.
Cost-effectiveness
Evaluate the overall cost-effectiveness of the metal filled adhesive. Consider factors such as the adhesive’s price, coverage area, and the long-term durability it offers. Balancing performance and cost will help you choose the most suitable adhesive for your project while staying within budget.
Conclusion
In conclusion, metal adhesive is a game-changer in the realm of bonding. Its unique formulation combines the strength and durability of metals with the convenience and versatility of adhesive.
By harnessing the power of metallic bonding, this remarkable adhesive opens up a world of possibilities in various industries and applications. From construction and manufacturing to automotive and electronics, metal adhesive provides unparalleled bonding strength and reliability. It allows for the creation of unbreakable bonds that withstand the test of time and deliver exceptional performance.
Embrace the power of metallic bonding with metal-filled adhesive and unlock a new level of strength and durability in your projects. Say goodbye to weak bonds and welcome the extraordinary power of metal-filled adhesive into your toolkit.