I. Introduction
Welcome to the fascinating world of adhesive bonding, where rubber meets rubber and forms unyielding connections. Rubber-to-rubber adhesive, a remarkable bonding agent, plays a crucial role in various industries, providing unmatched strength and versatility. In this article, we will delve into the intricacies of this adhesive, its myriad applications, and the pros and cons associated with its use.
Let’s dive into this peculiar topic and uncover the taste, health risks, and even unique uses of glue beyond its intended purpose.
II. Understanding Rubber-To-Rubber Adhesive
Definition and Composition
At its core, Rubber-To-Rubber adhesive is a type of bonding agent that creates a resilient bond between two rubber surfaces. It is composed of various chemical compounds that facilitate the adhesion process. Common components include elastomers, resins, tackifiers, and fillers. Each element plays a specific role in enhancing the adhesive’s performance.
Types of Rubber-To-Rubber Adhesive
1. Natural Rubber Adhesives
Derived from latex extracted from rubber trees, natural rubber adhesives are eco-friendly and exhibit excellent tackiness. They are commonly used in applications where biodegradability and sustainability are critical factors.
2. Synthetic Rubber Adhesives
Synthetic rubber adhesives are manufactured in laboratories and come in diverse formulations, making them suitable for specific applications. They offer superior performance in extreme conditions and have a longer shelf life than natural rubber adhesives.
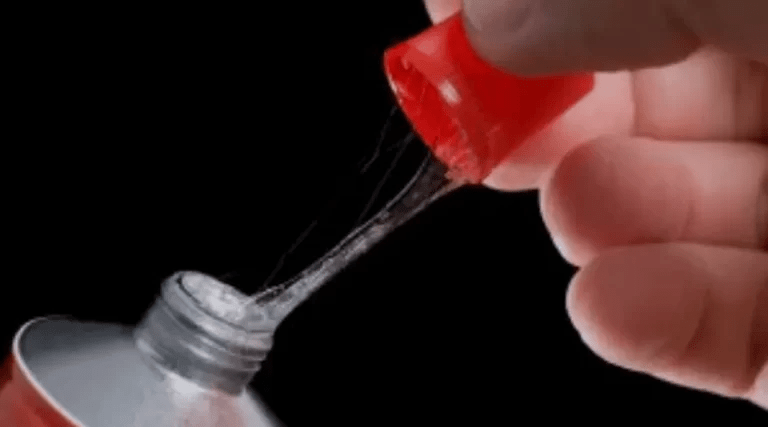
Working Principles and Chemical Reactions
When two rubber surfaces come into contact with the adhesive, the bonding process initiates through molecular interactions. The adhesive’s molecules form bridges between the rubber molecules, creating a strong and durable bond. The curing process involves the evaporation of solvents or the cross-linking of polymers, leading to a stable bond.
III. Applications of Rubber-To-Rubber Adhesive
Rubber-to-rubber adhesive has found extensive use in a wide range of industries due to its outstanding properties. Let’s explore some of its most prominent applications:
Automotive Industry
In the automotive sector, rubber-to-rubber adhesive plays a pivotal role in bonding rubber gaskets, weatherstrips, and seals. These bonds ensure that critical components are securely sealed, providing protection against water and other external elements, ultimately contributing to the vehicle’s durability and performance.
Electronics and Technology Sector
The electronics industry relies on rubber-to-rubber adhesive to attach rubber seals to electronic devices, preventing the ingress of dust and moisture. It is also used in the production of vibration-damping mounts, reducing noise and enhancing the lifespan of electronic components.
Footwear and Textiles
In the footwear industry, rubber-to-rubber adhesive is essential for bonding shoe soles, ensuring they remain intact under rigorous usage. Additionally, the adhesive is utilized in textile applications to create waterproof and airtight seams, enhancing the quality and functionality of various products.
Medical Applications
In medical equipment and devices, rubber-to-rubber adhesive is used to bond components like silicone tubing and rubber gaskets. These bonds maintain the integrity of the equipment, providing a sterile and safe environment for medical procedures.
Construction and Architecture
Rubber-to-rubber adhesive finds application in the construction industry for bonding rubberized roofing materials, sealing joints, and adhering rubber flooring. Its weather-resistant properties ensure long-lasting and reliable structures.
Marine and Aerospace
In marine and aerospace applications, rubber-to-rubber adhesive is employed for sealing windows, doors, and hatches. The adhesive’s ability to withstand extreme temperature variations and harsh environmental conditions makes it an ideal choice for these industries.
IV. Advantages of Rubber-To-Rubber Adhesive
Rubber-to-rubber adhesive offers a myriad of advantages, making it a popular choice for various bonding applications. Here are some key benefits:
Strong and Durable Bonds
The adhesive’s unique composition creates robust bonds that can endure mechanical stress and environmental factors without losing integrity. This strength ensures the longevity of the bonded components.
Flexibility and Resilience
Rubber-to-rubber adhesive remains flexible even after bonding, allowing the joined materials to move without compromising the bond. This property is particularly crucial in applications where flexibility is essential.
Enhanced Impact Resistance
The adhesive’s ability to absorb and disperse impact energy makes it suitable for applications where materials are subjected to sudden forces or vibrations.
Excellent Sealing Properties
Rubber-to-rubber adhesive creates effective seals, preventing the ingress of water, air, and other contaminants. This sealing capability is vital in applications where protection against environmental elements is essential.
Temperature and Weather Resistance
The adhesive’s resilience to temperature variations and weather conditions ensures that the bonded components maintain their integrity, even in extreme environments.
V. Limitations and Challenges
While rubber-to-rubber adhesive offers numerous advantages, it also faces some limitations and challenges that must be considered before usage. Let’s explore these drawbacks:
Environmental Concerns
Some rubber-to-rubber adhesives may contain volatile organic compounds (VOCs) and other chemicals that can contribute to air pollution and environmental degradation. Manufacturers are increasingly developing eco-friendly alternatives to mitigate these concerns.
Difficulty in Surface Preparation
Achieving a strong bond with rubber-to-rubber adhesive requires thorough surface cleaning and preparation. Contaminants such as dust, grease, or moisture can hinder the bonding process.
Aging and Degradation
Over time, some rubber-to-rubber adhesives may experience degradation due to exposure to UV radiation, temperature fluctuations, and chemical exposure. Regular maintenance and inspection are essential to ensure the longevity of the bond.
Limited High-Temperature Performance
In high-temperature environments, the adhesive may lose its bonding strength. For applications subjected to extreme heat, alternative adhesive options should be considered.
Compatibility Issues with Some Rubbers
Not all rubber compounds are compatible with rubber-to-rubber adhesive. It is crucial to test the adhesive’s compatibility with specific rubber materials before application.
VI. Best Practices for Using Rubber-To-Rubber Adhesive
To maximize the performance of rubber-to-rubber adhesive, certain best practices should be followed:
Surface Cleaning and Preparation Techniques
Before applying the adhesive, ensure that the surfaces are clean and free from contaminants. Use suitable cleaning agents and techniques to achieve optimum bonding results.
Correct Application and Drying Time
Follow the manufacturer’s guidelines regarding the application of the adhesive and the recommended drying time. Proper curing is vital for the formation of a strong and durable bond.
Proper Storage and Handling
Store the adhesive in a cool and dry place, away from direct sunlight and heat. Handle the adhesive with care, adhering to safety precautions and wearing appropriate personal protective equipment (PPE) when necessary.
VII. Comparative Analysis with Other Adhesives
Comparing rubber-to-rubber adhesive with other types of adhesives can provide valuable insights into its strengths and weaknesses:
Rubber-To-Metal Adhesive vs. Rubber-To-Rubber Adhesive
- Rubber-to-rubber adhesive excels in bonding rubber materials, while rubber-to-metal adhesive is designed for joining rubber and metal surfaces.
- Rubber-to-rubber adhesive offers greater flexibility and resilience, making it suitable for applications with dynamic movements.
Rubber-To-Rubber Adhesive vs. Cyanoacrylate Adhesive
- Cyanoacrylate adhesive (super glue) forms an instant bond, while rubber-to-rubber adhesive requires some curing time to achieve full strength.
- Rubber-to-rubber adhesive is more suitable for applications involving rubber materials, while cyanoacrylate adhesive works well with various substrates.
Rubber-To-Rubber Adhesive vs. Epoxy Adhesive
- Epoxy adhesive provides excellent strength and rigidity but may not be as flexible as rubber-to-rubber adhesive.
- Rubber-to-rubber adhesive is better suited for applications requiring vibration dampening and impact resistance.
VIII. Case Studies: Successful Implementations
Real-world applications of rubber-to-rubber adhesive showcase its efficacy and value:
Automotive Manufacturing: Bonding Rubber Gaskets
In the automotive industry, rubber gaskets play a critical role in preventing leaks and ensuring proper sealing. Rubber-to-rubber adhesive is used to bond these gaskets, creating a durable seal that can withstand harsh weather conditions and mechanical stress.
Electronics Assembly: Attaching Rubber Seals
In electronics manufacturing, rubber seals are utilized to protect sensitive components from dust, moisture, and other contaminants. Rubber-to-rubber adhesive is applied to attach these seals securely, ensuring the longevity and reliability of the electronic devices.
Footwear Industry: Shoe Sole Bonding
In the footwear industry, the bonding of shoe soles requires an adhesive that can withstand constant flexing and impact. Rubber-to-rubber adhesive provides the necessary flexibility and resilience to create a strong and lasting bond between the sole and the shoe’s upper.
IX. Safety and Health Considerations
When working with rubber-to-rubber adhesive, safety should be a top priority:
Handling Chemicals Safely
Follow the safety instructions provided by the adhesive manufacturer. Use the adhesive in a well-ventilated area and avoid direct contact with the skin or eyes.
Personal Protective Equipment (PPE) Guidelines
Wear appropriate PPE, such as gloves and safety goggles, to protect yourself from potential chemical exposure during application.
Safe Work Practices
Ensure that the work area is clean and well-organized. Clean up spills promptly and dispose of adhesive containers responsibly.
X. Future Trends in Rubber-To-Rubber Adhesive
As technology and innovation continue to advance, so does the field of rubber-to-rubber adhesive:
Advancements in Adhesive Formulations
Manufacturers are continuously developing improved adhesive formulations that offer enhanced performance, environmental friendliness, and reduced curing times.
Eco-friendly and Sustainable Alternatives
The industry is moving towards eco-friendly adhesive options, addressing environmental concerns and reducing the ecological footprint of adhesive applications.
Emerging Applications
As new industries and technologies evolve, the demand for rubber-to-rubber adhesive in innovative applications is likely to grow.
Conclusion
In conclusion, rubber-to-rubber adhesive is a remarkable bonding agent that creates strong and durable connections between rubber surfaces. Its versatility and resilience make it indispensable in various industries, from automotive to electronics, construction, and more.
The adhesive offers numerous benefits, including strong bonds, flexibility, impact resistance, and excellent sealing properties.
However, it also faces challenges such as environmental concerns and compatibility issues with certain rubber compounds. By following best practices and safety guidelines, users can optimize the adhesive’s performance and ensure safe application. With ongoing research and development, the future of rubber-to-rubber adhesive looks promising, with advancements in formulations and a focus on sustainable solutions.